次世代ドライクーラントシステム「DIPS」の導入前に|切削方法について考えよう!
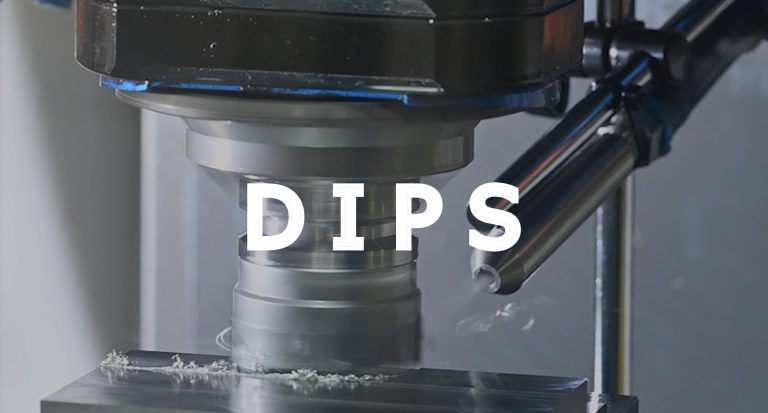
切削方法について考えよう!
切削液の代わりに極小径のドライアイスパウダーを使用する、従来の発想を覆すアイデアから誕生した次世代ドライクーラントシステム「DIPS(ディップス)」。
工作機械での加工は切削液を使う「ウェット加工(湿式切削)」と、切削液を一切使用しない「ドライ加工(乾式切削)」の大きく2つに分けることができます。今回はドライクーラントシステムである「DIPS」の特長や導入メリットをより深く理解するべく、「ウェット加工(湿式切削)」と「ドライ加工(乾式切削)」におけるそれぞれの違いについて考えてみましょう。
まず、環境問題やランニングコストの面を考慮すると、ウェット加工よりドライ加工が推奨されます。
ですが、被削材によっては潤滑性の高いウェット加工の方がより高い切削効率を得られるのも事実です。工具メーカーが販売している工具もウェット加工で使用するものが多いという点からも、一般的にはウェット加工がドライ加工よりも広く受け入れられていると言えるでしょう。
とはいえ、ウェット加工とドライ加工にはそれぞれ一長一短の特徴があります。
そのため、ユーザーは被削材ごとに加工方法や工具の種類、そしてどのようなクーラントが適しているのかを把握しておく必要があります。
では、ここからはウェット加工とドライ加工のメリット・デメリットを紹介していきます。
ウェット加工
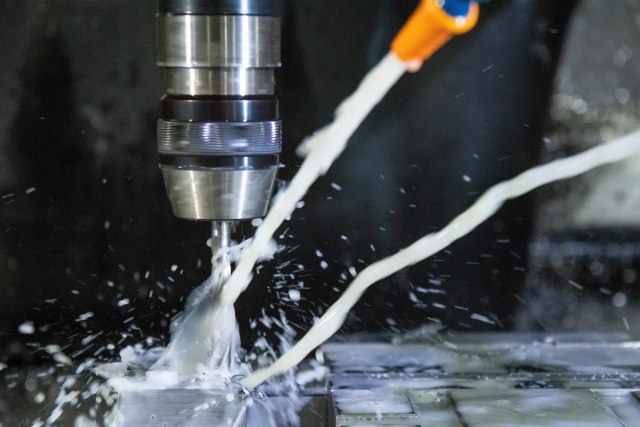
メリット
①ドライ加工に比べ、加工精度や表面仕上げ品質が上がる
②ドライ加工に比べ、冷却効果が高い
③ドライ加工に比べ、工具の種類が断然的に多い
デメリット
➊現在主流となっている水溶性切削油は潤滑性能を高める原液を使用するため、原液の仕入れや廃棄処理など様々な部分でコストが発生する
➋必ず洗浄工程が必要となる
➌油の汚れや臭いによる作業環境の悪化。作業者の健康面に悪影響がでる可能性も
➍切削液の濃度管理等、メンテナンスが必要になる
ドライ加工
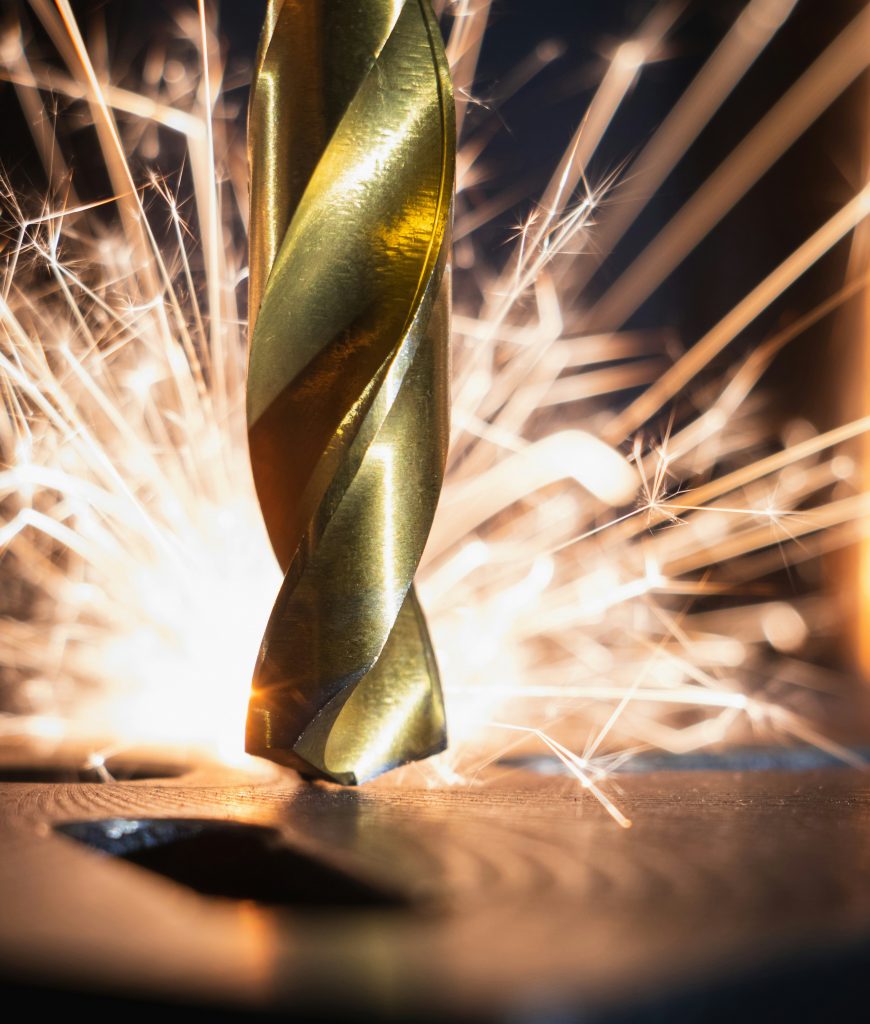
メリット
①ウェット加工に比べ、ランニングコストが抑えられる
②洗浄工程が不要
③作業環境が改善。健康面への悪影響を軽減できる
デメリット
➊ウェット加工に比べ、加工時に発生する熱の抑制力が低い
➋ウェット加工に比べ、加工精度が劣る
➌ウェット加工に比べ、専用工具の種類が少ない
➍潤滑性能が無いため、アルミ材などの柔らかく工具に溶着しやすい材料には適さない
一見、デメリットも多いように見えるドライ加工。
ですが、「DIPS」を活用することでメリットはそのままに、さらにデメリットを改善へと導いてくれます。
「DIPS」が導きだす、新たな切削『解』
ドライアイス方式のクーラントシステムである「DIPS」は、切削液を使用しないドライ加工の環境下でも効果的な冷却を実現!特に難削材の加工で効果を発揮します。これまでの切削加工の常識を覆し、新たな切削『解』へと導く可能性を秘めた独自のクーラントソリューションです。
「DIPS」の概要ですが、液化炭酸ガスボンベから液状の二酸化炭素を装置内に引き込みドライアイス粒子を生成します。その後ノズルから-79.8℃のドライアイス粒子と+60℃のエアーを同時に加工点に噴射することで「ワークの冷却」と「加工点周辺の低酸素濃度生成」の2つの効果を同時に実現します。
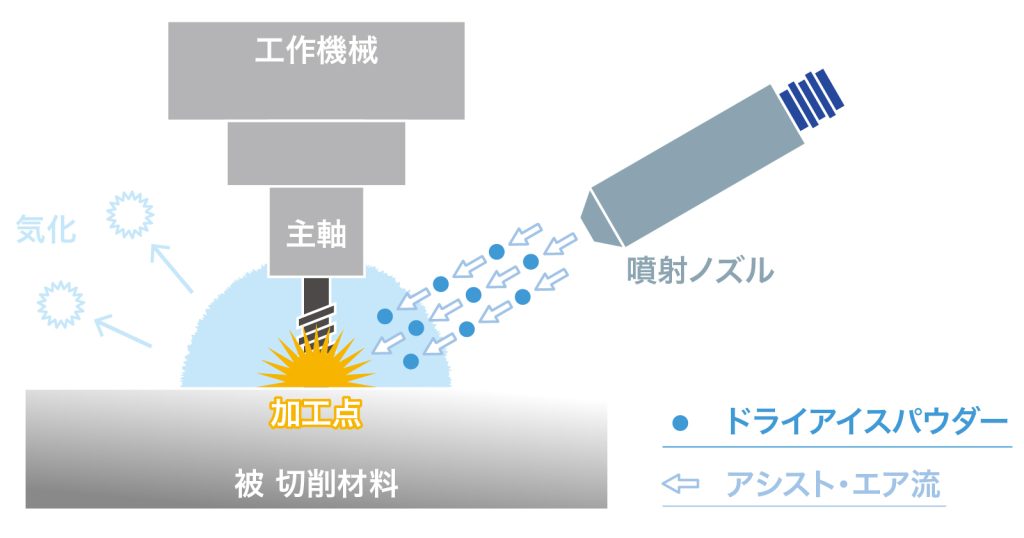
「DIPS」の存在は、従来のドライ加工に革新をもたらす新しい技術として注目されています!
本コラムをお読みいただいている方へ、加工手法を大きくアップデートする機会をご提供できるかもしれません。
次回は「DIPS」のドライアイスを応用した、加工工程へのアプローチについて解説していきます。
ご期待ください。