Meltio社の最新金属3Dプリンター「Meltio M600」に搭載のブルーレーザーを深堀り
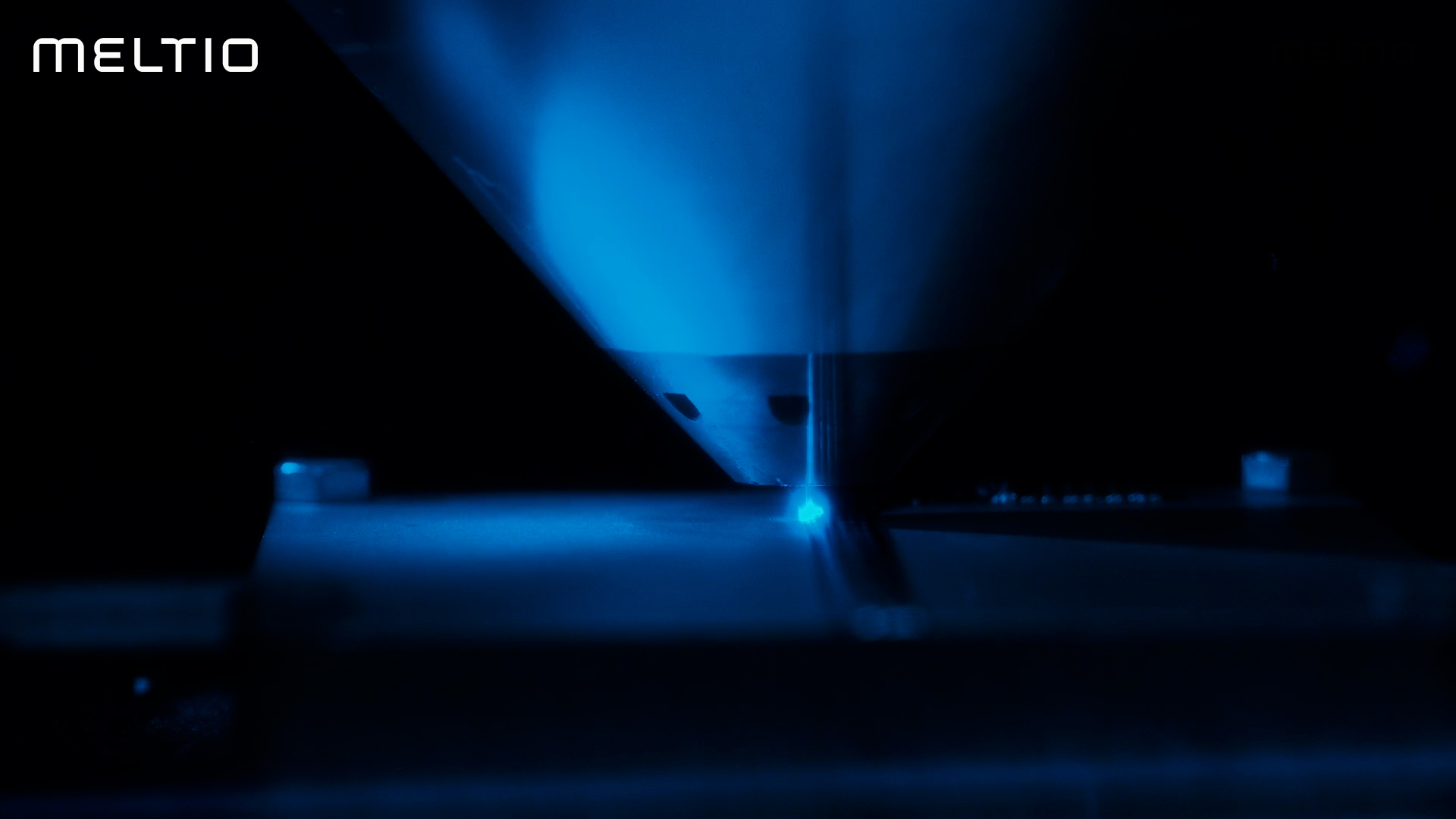
スペインの金属3DプリンターメーカーであるMeltio社は、このほどレーザーワイヤーDED方式を用いた第2世代の金属3Dプリンター「Meltio M600」をリリース。本機には独自にカスタマイズしたブルーレーザーシステムが採用され、広範囲な材料への対応が可能となりました。「Meltio M600」は、これまで以上に効率的な金属部品の造形を実現します。
近年ではレーザーワイヤーDED方式を採用する金属3Dプリンターが増え、さらに短波長のダイレクトダイオードレーザーの技術革新が進んでいます。今回は、ブルーレーザーの特徴とそのメリットやデメリット、そしてブルーレーザーを搭載した「Meltio M600」の特徴についても併せて紹介していきます。
Contents
ブルーレーザーとは
ブルーレーザーは別名「青色レーザー」とも呼ばれており、400nmから500nmの波長範囲の光ビームを放出します。従来の赤外線レーザーよりも銅や金といった非鉄金属への吸収率が高いため、近年非常に注目されているレーザーです。
ブルーレーザーのメリット
ワイヤーDED方式における高出力レーザーは、金属ワイヤーを溶かして積層造形する際に使用されます。従来の近赤外レーザーよりも高出力なブルーレーザーを使用する方が金属部品の積層造形において多くのメリットをもたらします。
多くの金属の場合、近赤外レーザーよりもブルーレーザーを効果的に吸収します。さらに波長が980nmから450nmに短くなることでより効率的に金属を溶かすことができ、高速な積層造形と部品ごとの総消費エネルギー削減を可能にしています。
特にアルミニウムや銅合金などの反射材料において、この効果は顕著に見られる傾向があります。これらの材料は需要が高く、従来の近赤外領域のレーザーでは造形が非常に難しいといわれています。
ブルーレーザーの活用は、レーザーワイヤーDED方式などのエネルギー効率の高い積層造形において、製造業の環境への影響を軽減します。
ブルーレーザーのデメリット
一方、デメリットも存在します。ブルーレーザーのコストは近赤外レーザーの数倍にも及ぶため、積層造形の分野で使用されるケースはまだまだ珍しいと言えます。
現在、ほとんどのレーザーワイヤーDED方式の造形ヘッドが高出力ファイバーレーザーを基に設計されています。ブルーレーザーが高コストとなる大きな要因は、kWクラスのブルーレーザーを制作するための難しいアライメントとファイバー結合です。
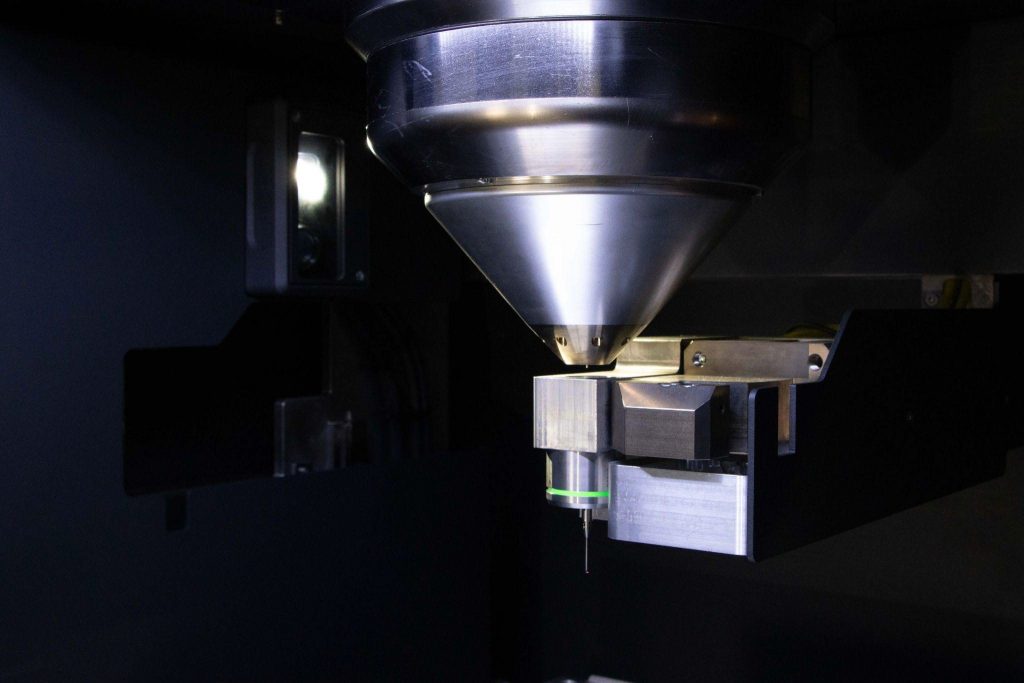
デメリットの改善:新しいシステムの誕生
Meltio社の主な目標は、レーザーワイヤー積層造形の大規模な産業利用です。異なるレーザー光源を導入し、既存の積層ヘッドにファイバーを結合するため、過去3年にわたってブルーレーザー光源を直接積層ヘッドに統合する新しい装置の開発に取り組みました。同時により多くの製造工程を内製化することで性能と柔軟性を向上させ、コストの削減を実現しました。
その結果、レーザーワイヤー積層造形のニーズに完璧に適合するレーザー光源をカスタマイズすることができました。より少ない光学素子で、かつブルーレーザー光源で期待される以上の高いウォールプラグ効率を実現しています。
レーザーを積層ヘッドに統合することで、すべての光学部品アセンブリを一つの密閉されたサブアセンブリに集中させることができるため、システムのメンテナンス中に壊れやすい光ファイバーを切断する必要がないというメリットをもたらします。
最後に、Meltio社がレーザーシステムを一から構築した最大のメリットは、手動でのレーザーワイヤーのアライメント調整が不要になったことです。レーザーの焦点をワイヤーに合わせる作業は手動で行われていたため、セットアップ間でのばらつきが生じ、追加のオペレーターのトレーニングが必要不可欠でした。
さらに、エネルギー分布を変化させ、ワイヤーのガイド精度を向上させることで、サービス後の再調整が必要なくなりました。また、異なる材料間のわずかなばらつきが許容された、工場にて調整済みの積層ヘッドを提供できるようになりました。
まとめ
ワイヤーDED方式を念頭に置いて直接レーザー光源を開発することで、オペレーターの手間とエネルギーの使用量を削減し、リーズナブルな価格を維持するシステムの提供が可能になっています。
Meltio社にとって、レーザーシステムとそれに対応する製造システムの開発は、複雑でありながらも、クリーンルームの設置、製造技術の習得、何千時間もの試験期間など、学びの多い経験でした。同社は、独自でカスタマイズしたブルーレーザーを搭載した「Meltio M600」が、製品の性能と信頼性をより高め、さらに最終造形品の炭素排出量を減らすという目標を達成するために必要不可欠であると考えています。
【関連記事】
・3DPCが国内総代理店を務めるMeltio社がスペインの「SME of the Year(中小企業大賞)」を受賞
・ワイヤーDED金属3Dプリンターで成形サイクルの冷却時間を半減する方法 | 3次元水管金型を造形するメリット
・異種金属接合、バイメタルとは | 金属3Dプリンターでバイメタル部品を造形するメリットを造形品とともにご紹介
製品紹介:Meltio M600
「Meltio M600」は、先行機種の「Meltio M450」と比較して造形面積が約4倍になり、鍛造品相当の強度を持った、より大きな金属部品を造形できます。また、チャンバー内をアルゴンガスで満たすよう設計されているため、より安定した造形を提供します。さらに、ホットワイヤー対応に加えて新たにブルーレーザーが搭載されたことで造形速度が速くなり、使用できる材料の選択の幅も広がりました。加えて、部品1個あたりのエネルギー消費量とコストの大幅削減を実現します。
先行機種と比較すると作業効率もはるかに上がっています。これまでは、プレートを設置するのに労力をかけていましたが、「Meltio M600」ではスライド式で設置できるため簡単に取り外しが可能です。新しいカメラ機能では造形の様子が鮮明にわかるためリアルタイムで監視ができます。加えて、ワイヤーカット機能により異なる材料を使用する際に安定した造形を提供するほか、ワイヤーのアライメント調整が不要になるなど「Meltio M600」は金属部品の造形を容易にしました。
対応可能な材料
・MIGワイヤーなどの既成材料
・銅合金
・アルミニウム
・ステンレス鋼:SUS 316L
・ステンレス鋼:SUS 308L
・ステンレス鋼:17-4PH
・工具綱:H11
・ニッケル合金:インコネル®718
・ニッケル合金:インコネル®625
・ニッケル合金:インバー
・炭素鋼:ER70S
・チタン合金:Ti-6AL-4V
機械仕様
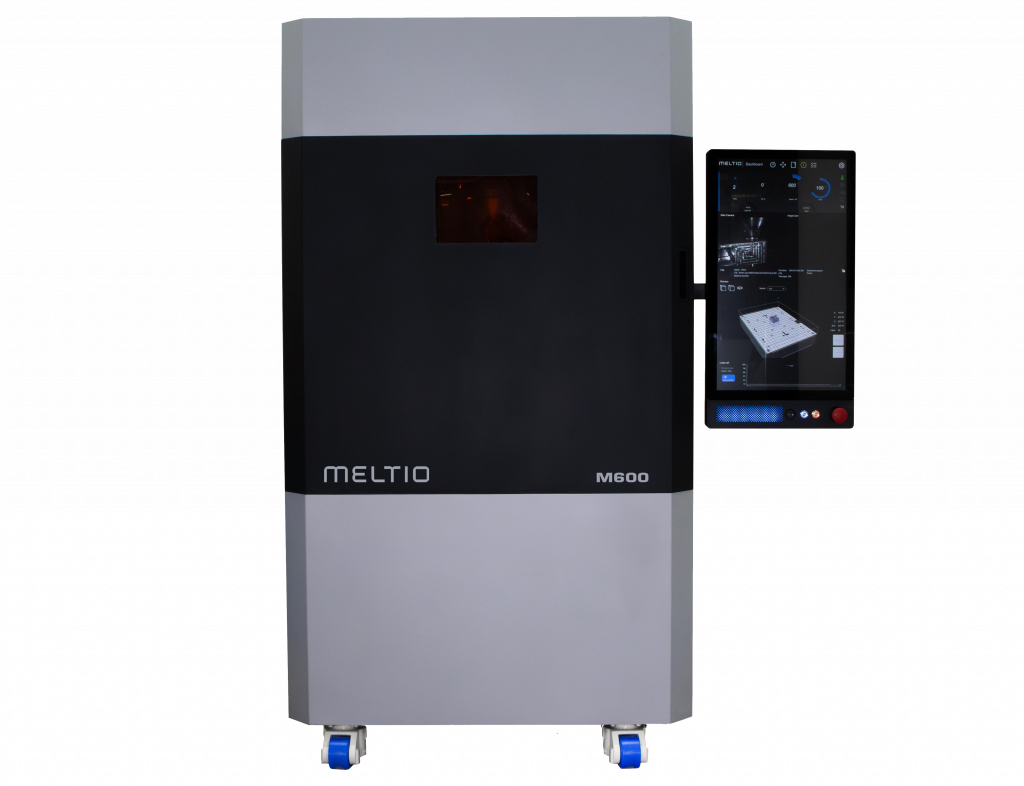
・造形エリア:300 x 400 x 580 mm
・本体サイズ:1050 x 1150 x 1950 mm
・本体重量:800~1000 kg(選択するオプションにより変動)
・レーザー:9つのダイレクトダイオードレーザー
・レーザー出力:1000 W
・レーザー波長:450 nm
・入力電源:三相 200 V
・消費電力:ピーク時 4~6 kW (選択するオプションにより変動)
・インターフェース:USB、イーサネット、ワイヤレス
・ソフトウェア:Meltio Horizon
・冷却:水冷式チラー
Meltio社について
Meltio社(スペイン)は2019年に設立され、知名度の高い産業界の顧客や大学などの研究開発機関を対象とした高品質の製品を開発・製造しています。レーザーメタルデポジション方式(DED)の技術を使用して、 高性能・手頃な価格・使いやすい金属3Dプリンターを開発・製造することで、金属における積層造形を次のレベルに引き上げます。現在では、世界中で300台以上のMeltio社製品を販売しています。
設計・開発から製造、後加工、品質評価まで一貫したサービスを提供
今回の記事は、3Dプリント技術を用いて設計から製造、後加工、品質評価までの一貫したサービスを提供している「株式会社3D Printing Corporation(3DPC)」が執筆しています。
3DPCでは、金属・樹脂合わせて10種類以上の3Dプリンターを取り扱っており、知見や経験が豊富な社員のもと、設計・開発から、製造、後加工、品質評価まで一貫したサービスを提供しています。また機器のご紹介も行っており、ご購入後は、1日から2日間のトレーニング、修理、メンテナンスのサポートを実施しております。
・メール経由:info@3dpc.co.jp
3DPCでは工場見学開催中!最先端技術を搭載した海外製3Dプリンターが10種類以上
具体的なイメージが持てるように、実際に3Dプリンターや造形品を見て触ることができる工場見学を開催しております。また、樹脂であれば無料で造形を承っており、金属の場合は50%オフで造形を行っています。※お申し込み時にデータをいただき、工場見学の際に造形品をお渡しいたします。
ご興味のある方は是非お問い合わせください。
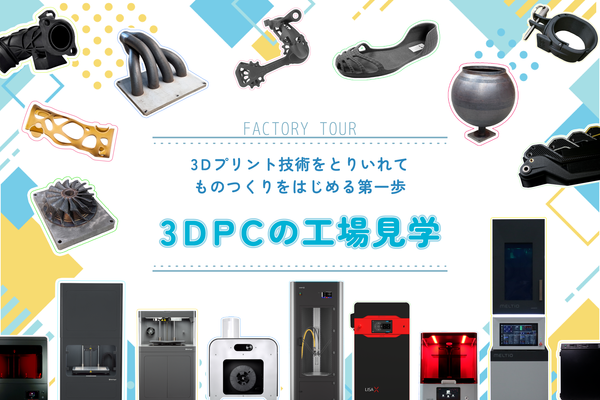