次世代ドライクーラントシステム「DIPS」の導入前に|「切削熱」と「ドライアイスの冷却効果」を知ろう!
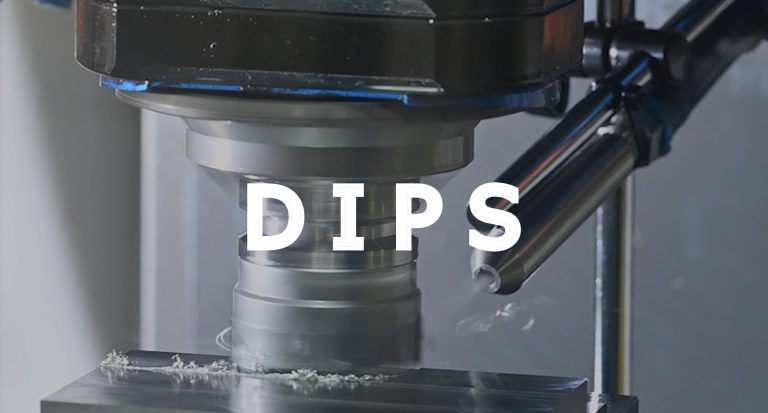
次世代のドライクーラントシステム「DIPS(ディップス)」の導入前に、知っておきたいシリーズ第3弾!
前回のコラムでは、「DIPS」の代名詞であるドライアイスの特性について解説しました。
ドライアイスの特性を応用することで、従来のドライ加工(エアーのみを当てながら切削する)以上の冷却効果が得られるということをご理解いただけたのではないでしょうか。
続く今回は「切削熱」にフォーカスを当て、「DIPS」がもたらす冷却効果について解説します。
切削熱とは
切削熱は、切削加工中に発生する熱エネルギーの総称です。
切削工具で材料を削る際には大きな力(切削力)が発生します。その後、力学エネルギーである切削力は熱エネルギーへ変化し、切削熱となります。
切削熱は発生する箇所によって「摩擦熱」「せん断熱」に分けられ、それぞれ特徴があります。
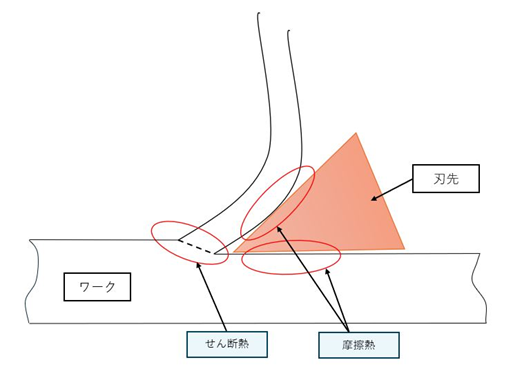
摩擦熱
「摩擦熱」とは刃先と被削材の摩擦によって発生する熱エネルギーです。
切削工具の刃先には、実際に削り出す「すくい面」と摩擦を抑えるための「逃げ面」があります。
「逃げ面」と聞くと摩擦熱が発生しないのではと思いがちですが、実際には「すくい面」「逃げ面」の両方で摩擦熱が発生します。
せん断熱
切削熱が最も高温となり、全体の60%ほどを占めるのが「せん断熱」です。
その温度は、なんと600~1000℃に達すると言われています。
ワークから切り屑が引き剥がされるタイミング(せん断)は非常に大きな切削力(力学エネルギー)が発生するため、せん断熱は摩擦熱以上に高温です。
チタンやインコネルなど、いわゆる難削材と呼ばれる素材の加工はより大きな切削力が必要となるため、発生するせん断熱もより高温となります。
切削熱による課題
摩擦やせん断により生じた熱は、切削工具とワークに留まります。
工具に切削熱が留まってしまうとその後の加工に支障をきたすだけでなく、工具の摩耗が早まるといった問題につながります。もちろんワークにも変形などの悪影響へとつながる恐れがあります。
そのため、切削時に発生した熱は即時に冷却することが求められます。
加工時の熱エネルギーが大きくなる難削材であるほど、効率的な冷却が重要とされています。
「DIPS」がもたらすドライアイス冷却
次世代ドライクーラントシステム「DIPS」は、ドライアイスを応用することで「摩擦熱」と「せん断熱」の両方を効率的に冷却します。
ノズルから-79.8℃のドライアイス粒子と+60℃のエアー(空気)を同時に噴射。ドライアイスが加工点周辺の酸素濃度を減少させることで加工点周辺が急速に冷却され、ワークや工具に留まる”熱”を抑制します!
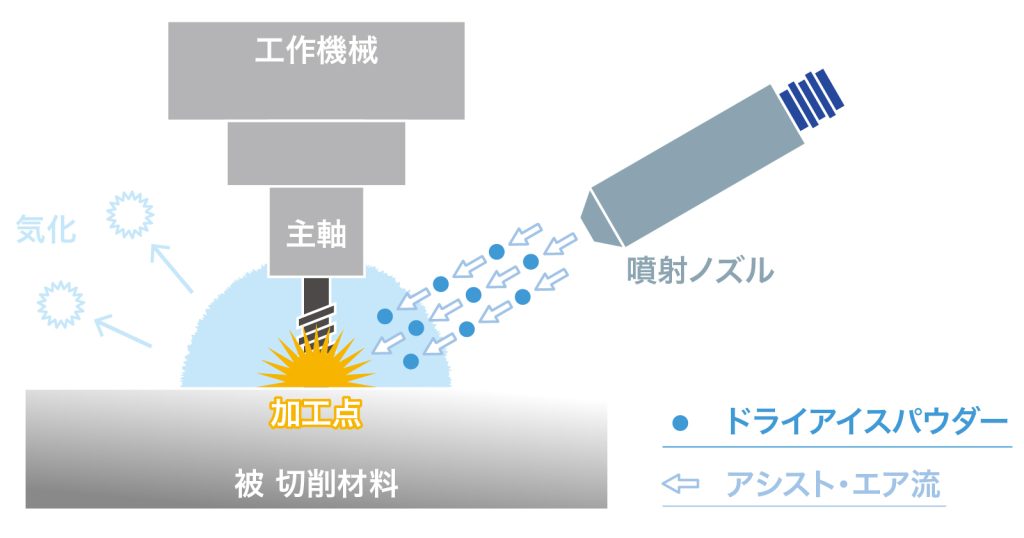
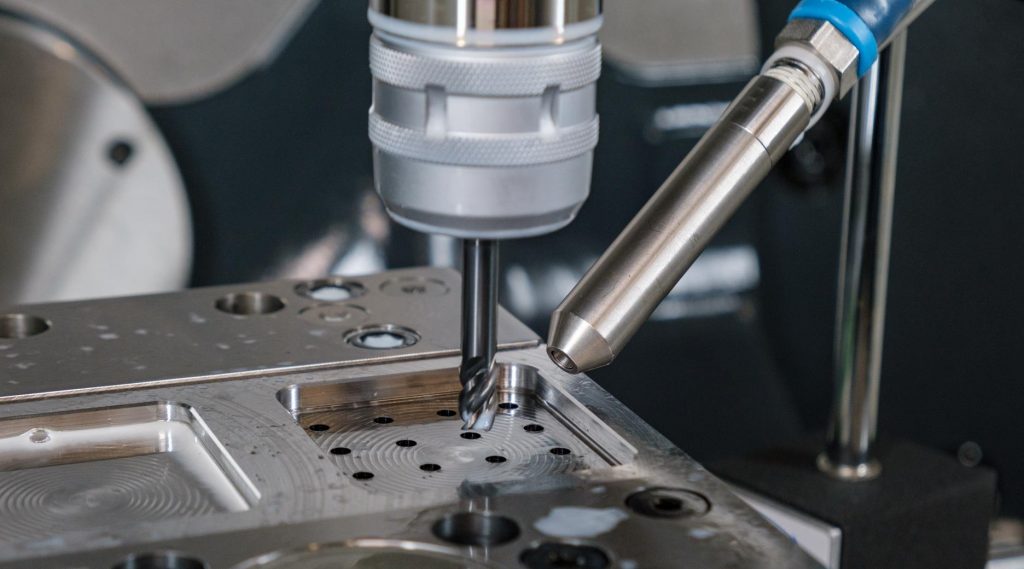
また「DIPS」は外付け設置なのでノズルの角度調整も自由自在です。
切削熱が発生する加工点周辺にピンポイントでドライアイスをヒットさせることができます。
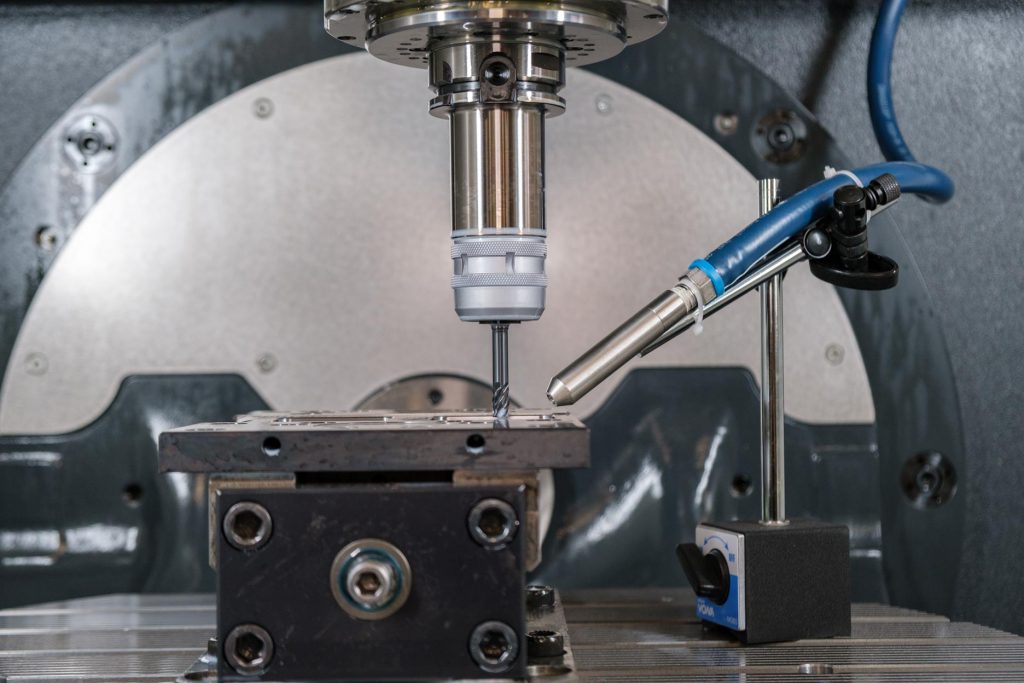
加工するワークや使用する工具が変わっても、安定して加工点にドライアイスを噴射することができる点が「DIPS」の大きな特長です!
まとめ
「切削熱」という、機械加工を行う上で避けては通れない課題の解決に向けた取り組みは、品質向上を図る上で非常に重要なピースです。
切削熱から工具とワークを守り、不良率の改善に貢献する「DIPS」。ドライアイスという新しい角度からドライ加工の改革を検討してみてはいかがでしょうか。
「DIPS」は従来のドライ加工に代わる技術として、切削熱の冷却を改善したいお客様におすすめしたいドライクーラントソリューションです!