工作機械とは?種類と機能を徹底解説
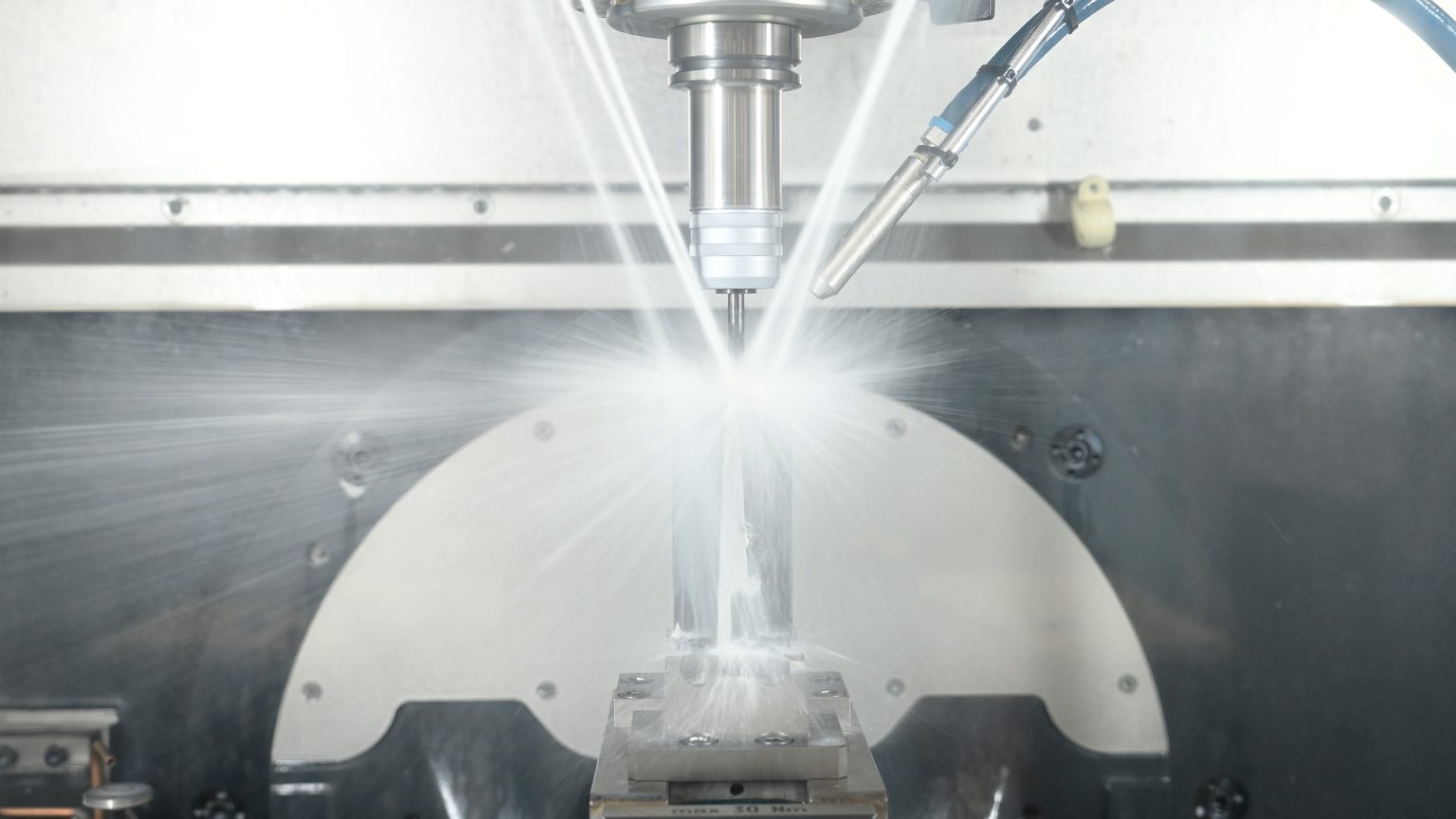
Contents
工作機械は高精度な工業製品の加工を支える「マザーマシン」
工作機械は、鉄やアルミニウムなどの金属の塊を刃物で削ったり穴をあけたりすることで不要な部分を取り除き、部品や金型などを作り上げる機械です。
工作機械は私たちの日々の生活に深く関わっており、工業製品の製造過程には必ず「工作機械」が使われています。世の中のありとあらゆる機械や部品が工作機械によって作られていることから、工作機械は「マザーマシン(母なる機械)」「機械を作る機械」とも呼ばれており、自動車や航空機、家電製品などのあらゆる工業製品の製造に不可欠な存在となっています。
工作機械の定義と重要性
私たちの身の回りを見渡すと、移動する際に利用する飛行機、電車、自動車、バイク、お店で見かけるプラスチック容器やキッチン用品などの小物類、毎日使っているスマートフォン(スマホ)やパソコン、ペットボトルなど身の回りにあるありとあらゆる製品が工作機械によって生み出されています。
工作機械を直接見ることはなくても、工作機械を使って作られた製品は誰もが必ず手に取っています。
まさに、工作機械は人々の生活において欠かすことのできない存在であると言えるでしょう。
「ものづくりに使う機械」という意味では、金型を使って薄い金属の板を成形するプレスなどの鍛圧機械、同じく薄い金属の板を切断するレーザー加工機などの板金機械、木材を加工するための木工加工機などもあります。しかし、日本工業規格(JIS)では工作機械を以下のように定義しています。
「主として金属の工作物を、切削、研削などによって、又は電気、その他のエネルギーを利用して不要な部分を取り除き、所要の形状に作り上げる機械。ただし、使用中機械を手で保持したり、マグネットスタンド等によって固定するものを除く。狭義であることを特に強調するときには、金属切削工作機械と表現することもある」
つまり、日本では金属製の材料(ワーク)を「削る」「磨く」「切断する」ことで目的の形状を作り上げる機械のことを「工作機械」と呼んでいます。
そして日本製の工作機械の高い精度は世界的に評価されており、国内で生産された多くの工作機械が海外の工場で活躍しています。また、工作機械の性能の優劣が生み出される製品の競争力を大きく左右し、その国の工業力全体にも大きく影響します。このため、各国とも工作機械産業を戦略的基幹産業と位置付け、その発展に力を尽くしています(出典:一般社団法人日本工作機械工業会ホームページ)。
このように現代の高度な産業社会において工作機械は技術革新の源泉であり、国際競争力を左右する重要な要素となっています。
工作機械で行う主な加工方法
工作機械で行う加工は多岐にわたりますが、主に以下の方法が挙げられます。
- 切削加工: 刃物(工具)を素材に押し当て、素材の不要部分を切り屑として除去(切削)する加工です。主に旋盤・フライス盤・マシニングセンタなどがこの加工を行います。金属加工の最も基本的な方法であり、形状を効率的に作り出すことができます。
- 研削加工: 砥石(微細な砥粒を結合剤で固めたもの)を高速で回転させ、素材の表面を研削(研磨)することで凹凸をなくし、非常に滑らかに仕上げる加工です。また、ミクロン単位の超高精度な寸法を出す際にも用いられます。主に研削盤がこの加工を行います。
- 放電加工: 電気的な放電現象を利用し、素材を溶融・蒸発・切断する加工です。工具と素材が物理的に接触しない非接触加工であり、電気を通す素材であれば硬度を問わずに加工できるのが特徴です。主に放電加工機がこの加工を行います。
これらの加工方法を使い分け、あるいは組み合わせて、複雑かつ高精度な部品が製造されます。
汎用機械とNC機械
工作機械は、その制御方式によって大きく「汎用工作機械」と「NC工作機械」の2種類に分けられます。この違いはものづくりの現場における自動化・生産性に大きな影響を与える要素となります。
■汎用工作機械
汎用工作機械は作業者がハンドルやレバーを直接操作して、刃物や素材の位置、移動スピードをコントロールしながら加工を行っていく機械です。

特徴:
- 手動操作: すべての操作を作業者が手動で行います。
- 高い熟練度を要求: 精度の高い加工を行うには、長年の経験と勘に基づいた熟練技術が不可欠です。加工する職人の腕が、製品の品質に直接反映されます。
- 柔軟な対応力: 急な仕様変更や1点ものの加工など、融通の利く対応が可能です。
- コスト: NC工作機械に比べて導入コストは低い傾向にあります。
汎用工作機械は使いこなすには相応の技術が要求されますが、ベテランの作業者がいる工場や試作品の製作、多品種少量生産の現場では今も現役で活躍しています。また、工作機械の操作の基礎を学ぶための教育現場(工業高校や高等専門学校、大学、各種職業訓練校など)では、その原理や基本的な操作方法を習得するために汎用工作機械が広く使われています。
■NC工作機械
一方、NC工作機械はプログラミングされた内容に基づき、数値制御によって自動で加工を行う工作機械です。工作機械に搭載されたNC(Numerical Control)装置は、NCデータ(またはNCプログラム)と呼ばれる専用のプログラムによって工作機械の動きを制御します。
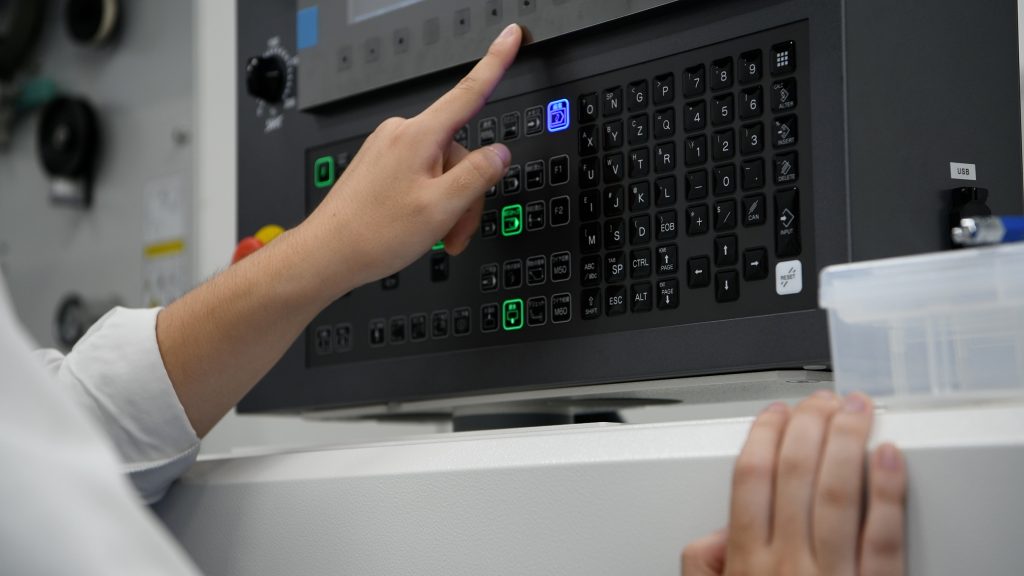
NC(Numerical Control:数値制御)の誕生: NC工作機械の概念は、第二次世界大戦後の米国で誕生しました。当時、航空機部品の複雑な形状を効率的かつ高精度に加工する必要があったことから、1952年にマサチューセッツ工科大学(MIT)が、紙のカードに穴を開けてデータを記録する「パンチカード」を用いて、記録された数値情報をもとに工具の動きを自動制御するシステムを開発したのがその始まりです。NC工作機械の誕生により、手作業では難しかった複雑な曲面の加工や高い繰り返し精度が実現されるようになりました。
CNC(Computer Numerical Control:コンピュータ数値制御)への進化: コンピュータ技術の発展に伴い、1970年代頃からNC装置に制御用コンピュータを内蔵した「CNC工作機械」が登場しました。CNC化によってプログラム作成や編集が柔軟に行えるようになっただけでなく、記憶容量の増加や通信機能が付加されることで飛躍的に機能が向上しました。なお、現在におけるNC工作機械はCNC工作機械が大半であり、両者の違いはほぼ無くなっています。そのため、単に「NC工作機械」と言えばCNC工作機械を指すのが一般的です。
■NC工作機械のメリット
自動化・省力化: 汎用工作機械ではすべて作業者が行っていた刃物や素材の位置・移動スピードのコントロール、回転速度のコントロール、刃物の自動交換などの作業をすべて自動で行うことができます。
人手による作業から解放され、作業者の負担が大幅に軽減されます。
高品質・高安定生産: 作業者によるスキルのばらつきを排除し、プログラミングされた通りの高精度な加工を安定して行うことが可能です。製品の品質が均一化され、不良品の発生を抑制できます。
複雑形状加工: 3次元CAD/CAMシステムと連携することで、曲面などの複雑な3次元形状も高精度に加工できます。
生産性向上: 24時間無人運転や多台持ち運転(1人の作業者が複数の機械を管理)が可能になり、生産効率を飛躍的に向上させることができます。
このようにNC工作機械には多くのメリットがあるため、現在では国内外の工作機械メーカーはNC工作機械を主力に生産を行っています。
工作機械は加工用途で選ぶ
工作機械は加工する形状や加工内容に応じて、非常に多様な種類が存在します。
そのため多くの製造現場では異なる複数の工作機械を組み合わせ、効率的にものづくりを行っています。ここでは、主要な工作機械の種類について詳しく解説します。
材料を回転させて削る工作機械「旋盤」
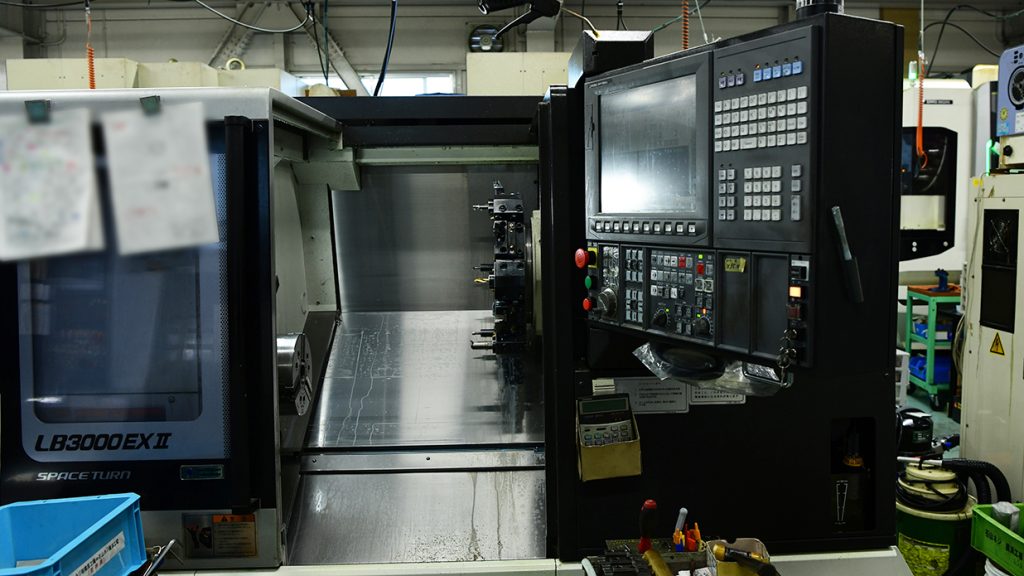
旋盤は、加工する材料を「チャック」と呼ばれる固定具に取り付け、材料を高速で回転させながら機械側に固定された「バイト」と呼ばれる刃物を押し当てて材料を削っていく工作機械です。材料が回転しながら削られていく様子は、こけしや茶碗を作る工程を思い浮かべると想像しやすいかもしれません。
旋盤で加工することを「旋削加工(せんさくかこう)」と呼びます。材料を回転させながら削っていくことから、主に円筒形状の材料を加工するのに適しています。なお、旋盤には機械を手動で操作する汎用旋盤(普通旋盤)とNC装置を搭載したNC旋盤の2種類があり、国内外の多くの工作機械メーカーが主力機種として生産を行っています。
旋盤の主な加工内容:
- 外丸削り: 材料の外周を円筒形に削る。
- テーパー削り:材料の両側を均等に先細りになるように(円錐状に)削る。
- 穴あけ: 材料に穴を開ける。
- 中ぐり: すでににある穴の経を広げたり、内面を滑らかにする。
- ねじ切り: 材料の外周や内周にねじ山を切る。
- 突切り: 材料を所定の長さで切断する。
- 面削り: 材料の端面を平らに削る。
旋盤の用途: シャフト・ボルト・ナット・フランジ・円筒部品など、自動車や航空機をはじめとしたあらゆる産業で使われる幅広い部品の加工で利用されます。
旋盤についてのさらに詳しい解説はこちら
工具を回転させて削る工作機械「フライス盤」
フライス盤は回転する刃物を材料に当てて、金属を削っていく工作機械です。
旋盤は材料が回転するのに対し、フライス盤は刃物が回転します。フライス盤で加工することを「切削加工(せっさくかこう)」と呼びます。
材料は「バイス」と呼ばれる道具で固定されます。加工中に材料が動かないようしっかり固定する必要があるため、フライス盤では四角形やブロック状の材料が多く使用されます。なお、フライス盤には汎用フライス盤とNC装置を搭載したNCフライス盤の2種類があります。
フライス盤の主な加工内容:
- 平面削り: 材料の表面を平らに仕上げる。
- 溝削り: 材料に溝(キー溝、T溝など)加工を行う。
- 段削り: 段差のある形状を加工する。
- 穴あけ: ドリルで材料に穴を開ける。
- ねじ立て:専用工具でねじ穴を切る。タップとも呼ばれる。
- 中ぐり: すでににある穴の経を広げたり、内面を滑らかにする。
- 側面削り: 材料の側面を削る。
フライス盤の用途: 金型・治工具・機械部品など、自動車や航空機をはじめとしたあらゆる産業で使われる幅広い部品の加工で利用されます。
フライス盤についてのさらに詳しい解説はこちら
数値制御で工具交換と加工を自動で行う工作機械「マシニングセンタ」
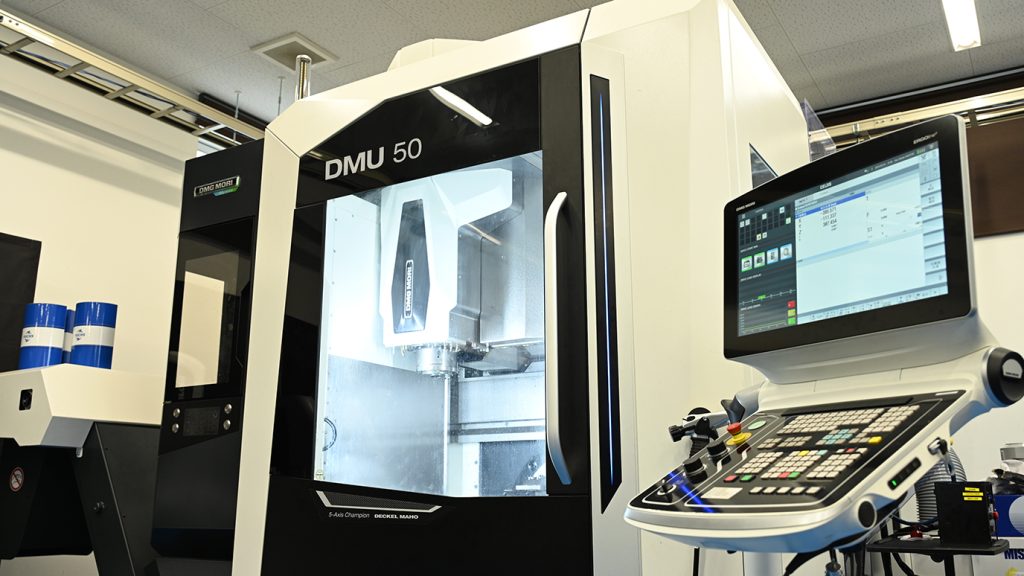
マシニングセンタは、フライス盤の機能をさらに進化させ、複数の加工を自動で行うことができる工作機械です。「マシニングセンター」や「MC」と記載されることもあり、口頭では「マシニング」と省略して呼ばれることも多い機械です。旋盤と同じく、マシニングセンタは国内外の多くの工作機械メーカーが主力機種として生産を行っています。
フライス盤との違い: マシニングセンタの最大の特徴は以下の2点です。
- 自動工具交換機能(ATC: Automatic Tool Changer): 複数の刃物(切削工具)を機械にセットしておくことで、加工中に必要な工具をプログラムの指令に基づいて自動で交換します。これにより、多種類の加工(穴あけ、フライス削り、中ぐり、タップなど)を、人手を介さず連続して行うことができます。
- NC装置による数値制御: フライス盤には汎用型もありますが、マシニングセンタは必ずNC装置(CNC)を搭載しており、プログラムによってすべての加工を自動で行います。
マシニングセンタの種類:
- 立形マシニングセンタ: 主軸が垂直方向に配置され、機械の上から下へ工具がアプローチします。重力による主軸のたわみが少なく安定した加工が行えます。様々なサイズの機械が各メーカーから販売されており、金型加工や部品加工で広く活用されています。
- 横形マシニングセンタ: 主軸が水平方向に配置され、機械の側面から工具がアプローチします。切り屑が自然に落下しやすいため切り屑の処理が行いやすく、パレットチェンジャー(APC)と組み合わせた自動化に適しています。機械のサイズは立形マシニングセンタと比較して大型化する傾向にあります。
- 門形マシニングセンタ: 門型構造の主軸を持ち、機械サイズも大型のものが多いことから大型ワークの加工に適しています。機械の剛性が高く、安定した重切削が可能です。
- 5軸マシニングセンタ: X・Y・Z軸の直線軸に加えて、A・B・C軸といった回転軸の制御が可能なマシニングセンタです。非常に複雑な形状の加工も段取り変えを必要とせず、ワンチャッキングで仕上げることが可能であり、加工時間の短縮と高精度化を実現します。
マシニングセンタの用途: 航空機・自動車・医療機器・半導体製造装置などの高精度かつ複雑な形状の部品製造、および金型に不可欠で、多くの製造現場で利用されています。
マシニングセンタについてのさらに詳しい解説はこちら
大物加工に欠かせない工作機械「中ぐり盤」
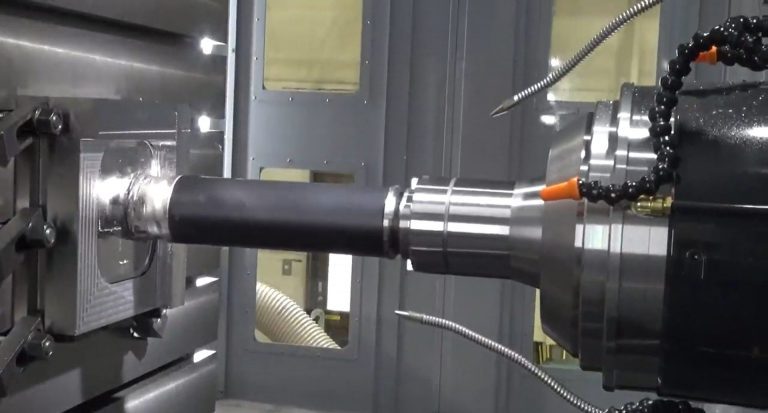
中ぐり盤は、主にドリルなどで事前に開けられた穴形状に対し、回転工具を使用してさらに穴径を大きく加工したり、穴の加工精度を高めたりするための工作機械です。
穴の径を大きくするだけでなく、真円度や位置精度、表面粗さなど、穴の加工精度が厳しく求められる場合に使用されるのが一般的です。特に大型の部品や穴の精度が重要な場合に威力を発揮します。
中ぐり盤の種類:
- 立中ぐり盤: 主軸が垂直方向に配置され、機械の上から下へ工具がアプローチします。重力による主軸のたわみが少なく安定した加工が行えます。また、横中ぐり盤と比較して省スペースに設置できるという特徴があります。
- 横中ぐり盤: 主軸が水平方向に配置され、機械の側面から工具がアプローチします。切り屑が自然に落下しやすいため切り屑の処理が行いやすいという特徴があります。
- ジグ中ぐり盤(ジグボーラー): 治具(加工物を固定し、工具の位置を正確にガイドする道具)の中ぐり加工を高精度に行うために開発された経緯を持つ機械です。現在では治具の加工に留まらず、非常に高い位置精度や真円度が求められる精密部品の加工で幅広く使われています。
マシニングセンタとの違い:マシニングセンタはATC(工具自動交換機能)を備え、1台で様々な切削加工が可能です。そのため汎用性が高く、生産性に優れた機械と言えます。一方、中ぐり盤は穴加工、特に大型ワークの穴加工に強みを持っており、近年ではマシニングセンタ、中ぐり盤がそれぞれ進化し両者の機能が近づいてきていますが、現在でも非常に高い精度が求められる穴加工では中ぐり盤がマシニングセンタを凌ぐ能力を発揮しています。
中ぐり盤についてのさらに詳しい解説はこちら
マシニングセンタと旋盤が一体化した工作機械「複合加工機」
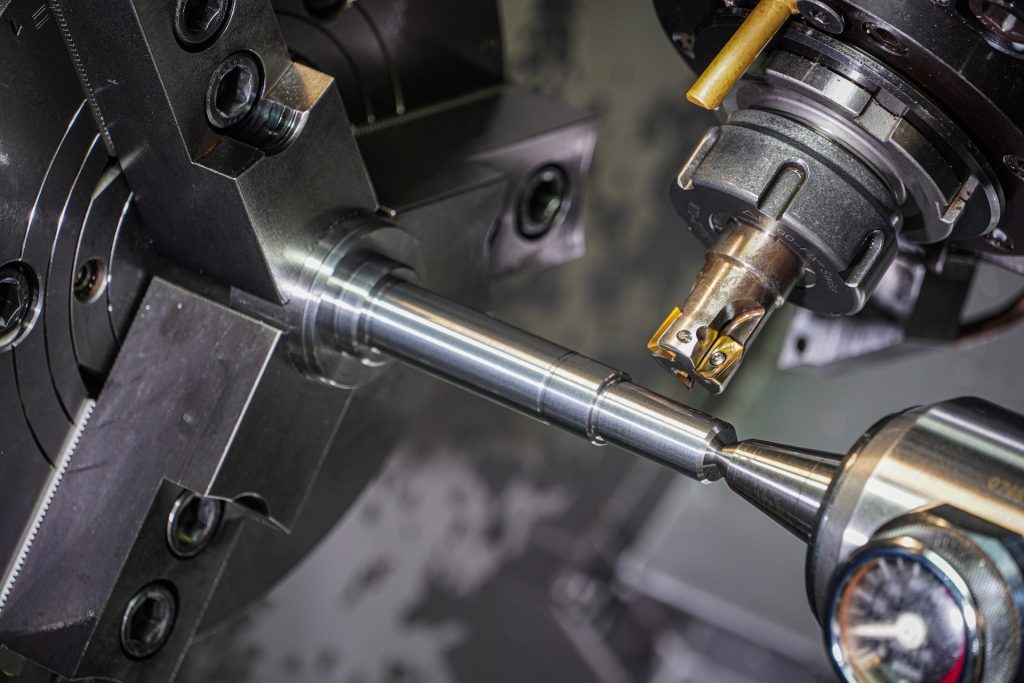
複合加工機は、旋盤が持つ旋削機能と、マシニングセンタが持つ切削機能(ミーリング機能)の両方を併せ持った工作機械です。かつては旋盤をベースにした機械が多かったことから「複合旋盤」「ターニングセンタ」と呼ばれることもありますが、最近ではマシニングセンタに旋削機能を付加した複合加工機も数多く登場しています。
特徴:
工程集約と生産性向上: 旋削加工と切削加工の異なる工程が必要な製品を加工する場合、通常は旋盤とマシニングセンタ(もしくはフライス盤)の2台の工作機械が必要となります。しかし、複合加工機であれば、これらの異なる2つの工程を1台の機械で完結できます。
加工精度の維持: 1台の機械で完結できるということは、一度機械に固定した材料を加工途中で取り外し、別の機械に固定し直す必要が無くなります。材料を外して固定し直す(掴み替える)と、わずかではありますがどうしても中心位置や基準位置がズレてしまう可能性があります。このことが加工する製品の精度に影響してきますが、複合加工機を使用すればそういった問題がクリアされ、高精度を維持できます。
省スペース化: 複数の機械を設置するスペースが不要になるため、工場内の限られたスペースを有効活用できます。
段取り時間短縮: 機械間のワーク搬送や段取り作業が不要になるため、全体のリードタイムが短縮されます。
用途: 自動車部品、航空機部品、医療機器部品、油圧・空圧部品など、複数の加工工程が必要な複雑形状の部品の加工に非常に有効です。
複合加工機は、省スペース化・工程集約・製品精度の維持という多くのメリットがあることから導入する企業が拡大しており、複合加工機を生産する工作機械メーカーもまた同様に拡大しています。
複合加工機についてのさらに詳しい解説はこちら
精密仕上げには必須の工作機械「研削盤」
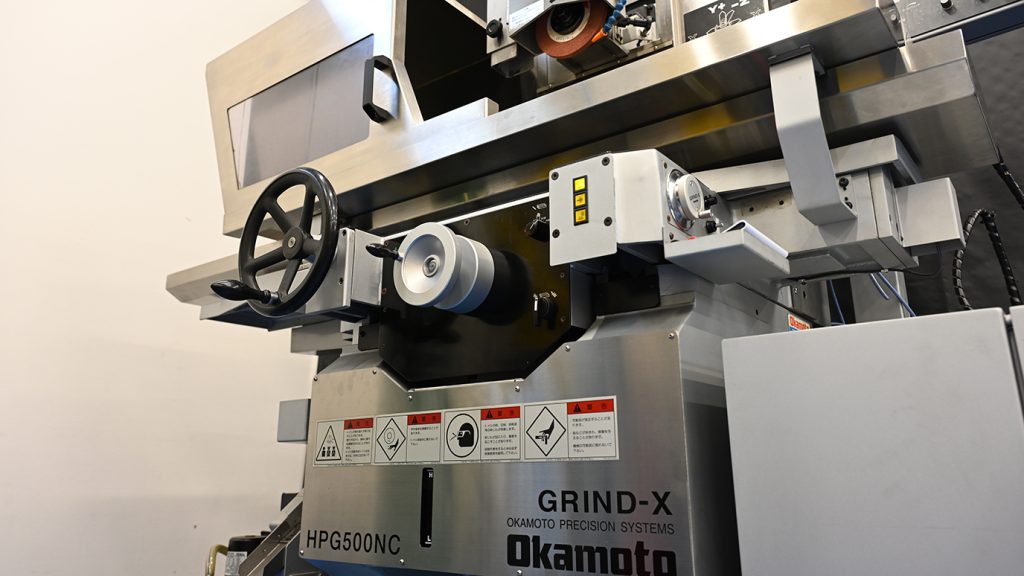
研削盤は、砥石(といし)を使って材料の表面を削る機械です。高速回転する砥石を材料の表面に押し当て、微細な砥粒で少しずつ表面を削っていくことで、材料の表面を非常に滑らかに仕上げることができます。機械加工において、製品形状を仕上げる最終工程で使用されることの多い工作機械です。
研削盤で加工を「研削加工(けんさくかこう)」と呼びます。切削加工が刃物で「削る」のに対し、研削加工は砥石で「磨く」というイメージです。そして研削盤は加工する製品の形状や種類に応じた様々な機種が開発されています。
特徴:
- 超高精度な仕上げ: ミクロン台からナノメートルレベルの寸法精度を実現し、鏡面のような非常に滑らかな表面仕上げを実現します。
- 高硬度材料の加工: 焼入れ後の材料やセラミックなど、通常の刃物では加工が困難な非常に高硬度な材料も加工できます。
研削盤の種類:
- 平面研削盤: 素材の表面を高精度に仕上げる研削盤です。金型加工を行う前の素材の面だしなどに使われます。
- 円筒研削盤: 円筒形状の素材の外径や内径を高精度に仕上げる研削盤です。シャフト・ベアリング・ゲージなどの製作の際に使われます。
- 内面研削盤: 穴形状の内側を精密に仕上げる研削盤です。ベアリングやシリンダーの内面仕上げなどに使われます。
- センタレス研削盤: 素材を機械の両端で支持せず、砥石・調整車・ブレードの3点で支えながら仕上げる研削盤です。大量生産に適しており、長尺物の加工にも対応が可能です。
- 工具研削盤: ドリルやエンドミルなどの切削工具を製造したり、再研磨したりするための研削盤です。
- 成形研削盤: 特殊な形状の砥石を用いて、複雑な輪郭や曲面を仕上げる研削盤です。
用途: 精密金型をはじめ、航空機部品、自動車のエンジン・トランスミッション部品、ベアリング、光学レンズ、半導体製造装置部品など、非常に高い寸法精度と表面品質が求められる分野で広く利用されています。
研削盤についてのさらに詳しい解説はこちら
難削材加工に効果を発揮する工作機械「放電加工機」
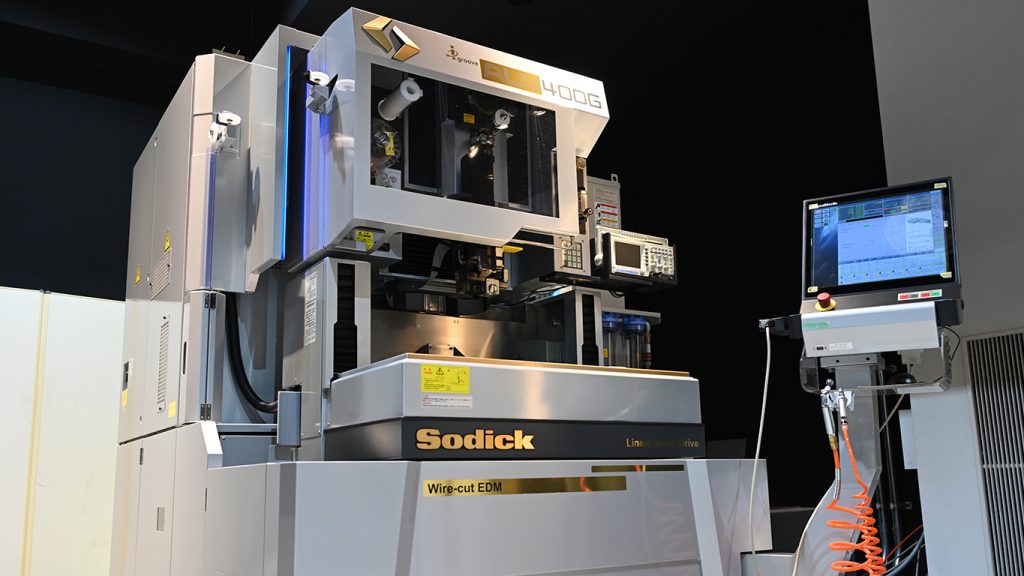
放電加工機は、電気エネルギーを利用して、材料を溶融・蒸発させることで少しずつ除去したり、糸ノコで切断するように加工する工作機械です。英語ではEDM(Electrical Discharge Machining)と呼ばれます。
特徴:
- 非接触加工: 放電加工は工具(電極)と被加工物が物理的に接触しないため、機械的な負荷や振動、ひずみが発生しません。
- 硬度不問: 電気を通す材料であれば、金属の硬さに左右されずに加工が可能です。このため、難削材(なんさくざい)と呼ばれる非常に硬い金属(超硬合金、焼入れ鋼、チタン合金、インコネルなど)の加工や、通常の切削では難しい非常に細い穴、深い穴、鋭いコーナーの加工に利用されています。
- 加工速度: 素材を少しずつ加工していくため、旋盤やマシニングセンタなどのように工具を使って物理的に削る加工方法よりも時間はかかります。しかし、複雑な形状や高硬度材の加工においては他に代替手段がない場合が多く、放電加工に優位性があります。
放電加工機の種類:
ワイヤ放電加工機: 真鍮などの細いワイヤー線(直径0.05mm〜0.3mm程度)を電極として使用し、ワイヤーに電流を流しながら素材を糸のこぎりのように切断していく加工方法です。
形彫り放電加工機: 加工したい形状と同じ形状に作られた電極(銅やグラファイト製)を素材に繰り返し近づけて放電を起こし、電極の形状を被加工物に「彫り込む」加工方法です。
用途: プラスチック(樹脂)金型やプレス金型などの製作をはじめ、超硬素材の加工、航空機部品などの微細穴加工、医療機器部品など、高精度かつ高硬度な材料の加工が求められる分野で広く利用されています。
放電加工機についてのさらに詳しい解説はこちら
様々な歯車を精度良く加工する工作機械「歯車加工機」
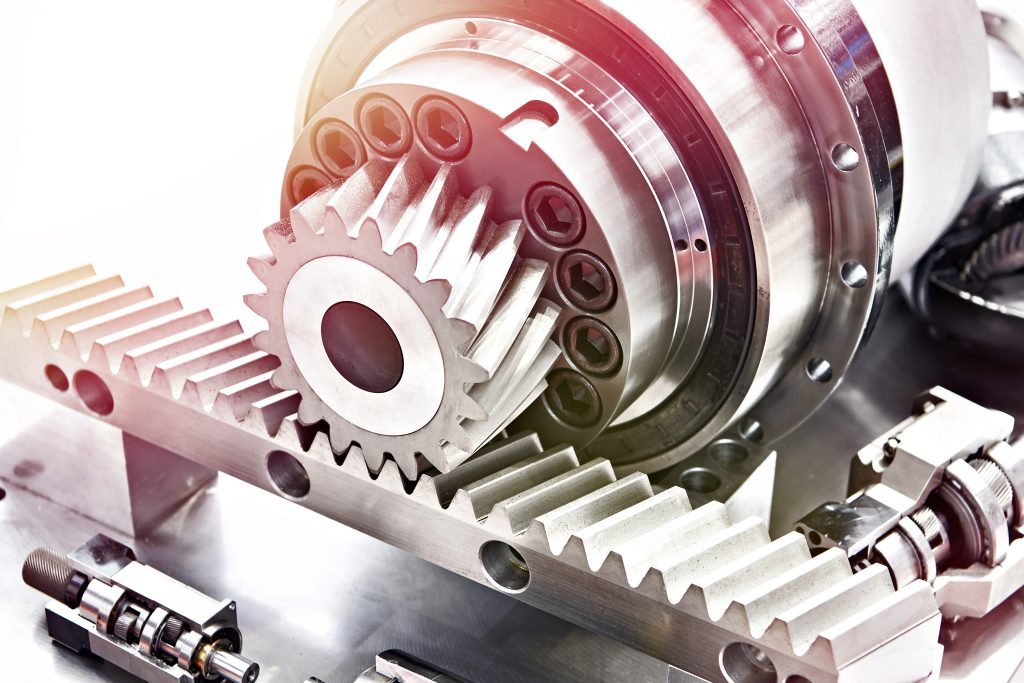
歯車加工機は、その名のとおり歯車を作るための専用の工作機械です。歯車の「歯」の部分を加工することを「歯切り」と呼ぶため、「歯切り盤」とも呼ばれます。
歯車は機械の動きを伝える上で極めて重要な部品であり、高い精度が求められます。歯車加工機は、この歯車の形状やピッチ(歯と歯の間隔)を正確に作り出すために特化した工作機械です。
主な種類:
- ホブ盤: 「ホブ」と呼ばれるらせん状の専用刃物を回転させながら、連続的に歯を削り出していく機械です。ウォームギアの原理を応用した創成(そうせい)加工により、高精度な歯車を効率よく量産できます。
- ギヤシェーパ: ラック状やピニオン状の刃物を上下させながら、材料を回転させて歯を切り出す加工機です。内歯車(インターナルギア)や段付き歯車など、ホブ盤では加工が難しい形状の歯車加工に用いられます。
- ギヤスカイビング盤: ギアスカイビングマシンとも呼ばれ、素材と工具を同期回転させながら、歯車を徐々に噛み合わせるように加工する機械です。ギヤシェーパと同様に、ホブ盤では難しい内歯車(インターナルギア)が加工できる点が特徴です。
- 歯車研削盤: 歯車の精度をさらに高めるために、歯切り後の歯車を研削する専用の研削盤です。
用途: 自動車のトランスミッションや航空機のギアボックス、建設機械、ロボットなど、高い信頼性と伝達効率が求められるあらゆる機械の駆動部に使用される様々な歯車の製造に利用されています。
歯車加工機についてのさらに詳しい解説はこちら
大量生産に欠かせない工作機械「成形機」
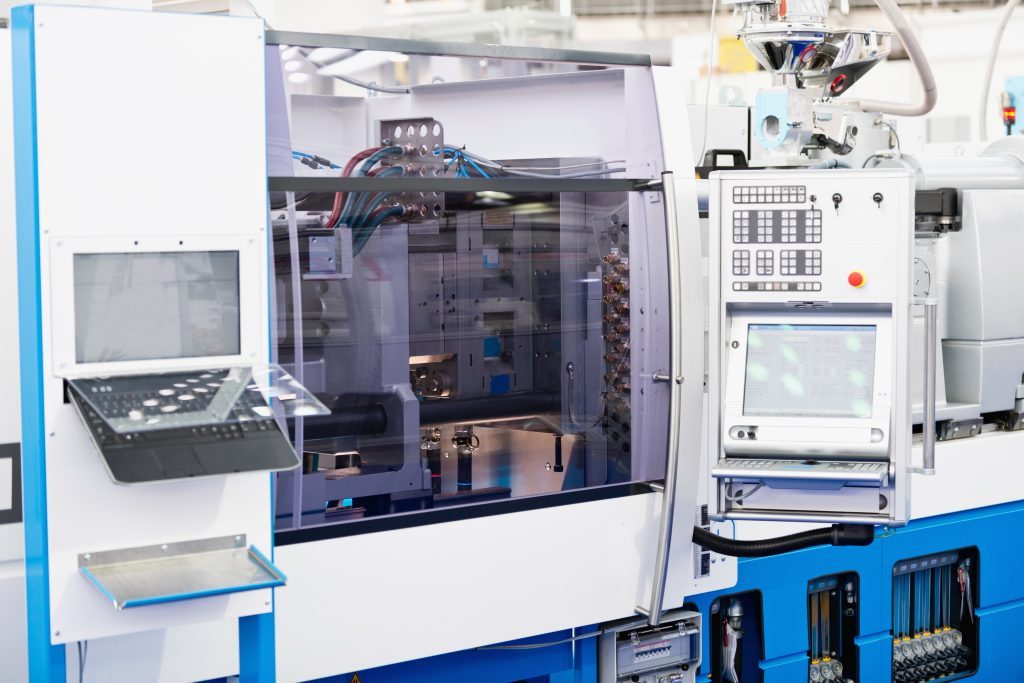
成形機は、主に樹脂(プラスチック)を原料として、身の回りで使われている様々なプラスチック製品を作り出す機械です。厳密にはJISの定義する「工作機械(金属加工)」からは外れますが、製造業界で活躍する重要な機械であるため、ここで解説します。
加工方法: 原料である樹脂材(プラスチックのペレットなど)を高温で溶かした後、溶融した樹脂を金型に流し込み、圧力をかけて成形することで製品を作りだします。金型は前述の工作機械(特にマシニングセンタや放電加工機)によって作り出されます。
主な種類:
- 射出成形機: 最も広く使われている成形機です。高温で加熱して溶かした樹脂材を、閉じた金型の中に高い圧力をかけて注入し、冷却して固めた製品を自動的に取り出す機械です。複雑な形状のプラスチック製品・部品を大量生産するのに適しています。
用途: 自動車部品、家電製品の筐体、医療用具、食品容器、日用品、スマートフォン部品など。
- 押出成形機: 樹脂材をヒーターで溶かし、スクリューで押し出しながら、ところてんのように押し出すことで、連続的に一定断面の製品(パイプ、シート、フィルム、ケーブル被覆など)を成形する機械です。
用途: 塩ビ管、ビニールハウス用フィルム、電線被覆、ストローなど。
- ブロー成形機: 溶かした樹脂材を筒状に押し出し、それを金型で挟み込んだ後、内側から空気を入れることで膨らませた樹脂を金型に押し当て、空洞状の製品を作り出す機械です。
用途: ペットボトル、灯油缶、シャンプーボトルなどの液体容器など。
- 真空成形機/圧空成形機: 加熱して軟化した樹脂シートを型に密着させ、真空や空気圧を利用して成形する機械です。
用途: 食品トレー、ブリスターパック、自動車の内装部品など。
成形機はほぼすべてのプラスチック製品の製造に利用されており、私たちの生活に不可欠な存在となっています。
成形機についてのさらに詳しい解説はこちら
工作機械はここまで進化!
近年における工作機械は、単に金属を削るだけの機械ではありません。IoT、ロボット、AI技術との融合により、ますます高度化・知能化が進んでいます。
スマートファクトリー化: 工作機械に搭載された多数のセンサーから得られるデータをリアルタイムで収集・分析し、稼働状況の監視、故障予測(予知保全)、生産プロセスの最適化、品質管理の向上を行う「スマートファクトリー」の概念が急速に普及しています。稼働率の向上、コスト削減、品質安定化など様々なメリットが期待できます。
AIと機械学習: AIが過去の加工データや熟練工のノウハウを学習し、最適な加工条件の自動設定や、工具摩耗の予測、異常検知などを行う技術開発が進んでいます。これにより経験の浅い作業者でも高精度な加工が可能になったり、熟練工の技術をデジタル化して継承することが可能になります。
アディティブマニュファクチャリング(AM)との融合: 「削って作る(除去加工)」の工作機械に対し、材料を積み重ねて形を作る「アディティブマニュファクチャリング(AM)」の技術が近年発展してきています。金属3Dプリンターで造形後、マシニングセンタによる切削加工で仕上げるという、AMと切削加工のハイブリッド機も登場。複雑な内部構造を持つ部品や難加工材の製造など、新たなものづくりの可能性を切り拓いています。
デジタルツイン技術の活用: 工作機械や工場と全く同じデジタルモデルを構築し、仮想空間上で加工シミュレーションなどが行える「デジタルツイン」技術が発展しています。バーチャル空間で生産計画の最適化を行うことで、試作回数の削減や開発期間の短縮、リスクの低減などが図られます。
工作機械はキカイカタログ
「キカイカタログ」には、ものづくりの現場で活躍する様々な工作機械の最新情報が多数掲載されています。国内外の工作機械の情報を見るだけではなく、様々なメーカーの工作機械をウェブサイト上で並べて比較することで、新しい気づきがあるかもしれません。
最新の工作機械の導入をご検討される際は、ぜひ「キカイカタログ」をご活用ください。
「キカイカタログ」は製造現場で働く皆様にとって、ベストな1台との新たな出会いをご提供いたします。
工作機械に関する展示会情報も、下記の専用ページよりご覧いただけます。
開催予定の展示会や過去の開催実績など、さまざまな情報を随時更新しておりますので、ぜひご活用ください。